Kierreniittien asennuksen tarkastaminen 3D-kuvauksella
Erilaisten tuotannon asennusvaiheiden automaattinen tarkastus on entistä tärkeämpi osa kustannustehokkuuden parantamista. Tässä demonstraatiossa kokeiltiin 3D-kuvauksen mahdollisuuksia kierreniittien asennuksen tarkastamisessa. Moniulotteisten kappaleiden ja osien tarkastaminen ei välttämättä aina onnistu 2D-konenäöllä, mutta 3D-konenäkö voi tuoda juuri oikean ratkaisun.
Lähtötilanne
Tehokas konepaja -hankkeen aikana useammissa yrityksissä tuli esiin tarve tarkastaa moniulotteisten tuotteiden eri asennusvaiheiden laatua. Tätä lähdettiin kokeilemaan alumiinikappaleisiin asennettujen kierreniittien tarkastuksen avulla. Demonstraatiolla oli tarkoitus selvittää, voidaanko 3D-kuvauksella tunnistaa kierreniittien asennuksen jälkeen, ovatko kaikki kierreniitit paikoillaan. Kappaleet, joihin kierreniittejä asennetaan, ovat kiiltävää alumiinia ja asennettavat kierreniitit ovat myös kiiltävää metallia. Monissa vastaavissakin kohteissa tarkastuksen tulisi olla automaattista ja suhteellisen nopeaa. Tässä esimerkissä kappaleiden muoto ja koko vaihtelee riippuen valmistettavasta tuotteesta.
Kokeilun määrittely
Demonstraatiossa kokeiltiin RoboAI-laboratorion 3D-kuvausjärjestelmiä soveltuvin osin testiin saatujen kappaleiden kuvaamiseen ja kierreniittien asennuksen tunnistamiseen.
Tekniikat
Testikappaleet (kuva 1) ovat kiiltävää alumiinia ja kierreniitit kiiltävää metallia. Toisessa kappaleessa niitit ovat asennettuna ja toisesta ne puuttuvat. Testikappaleisiin tutustumisen jälkeen todettiin, että RoboAI-laboratoriossa käytettävissä olevista 3D-kuvaustekniikoista parhaiten soveltuva on rakenteelliseen valaisuun perustuva 3D-kuvaus Gocator 2380 -kameralla (https://tehokaskonepaja.samk.fi/3d-konenako/3d-konenakoteknologiat/). Gocator 2380 hyödyntää 3D-kuvauksessa laserviivaa, jonka muodonmuutoksia kohteessa kuvataan. Kiiltävät kappaleet ovat ongelmallisia 3D-kuvauksessa ja Gocator 2380 ei ole poikkeus, mutta se on nopeudeltaan ja ohjelmiston työkaluiltaan soveltuvin tehtävään tarkasteluun.
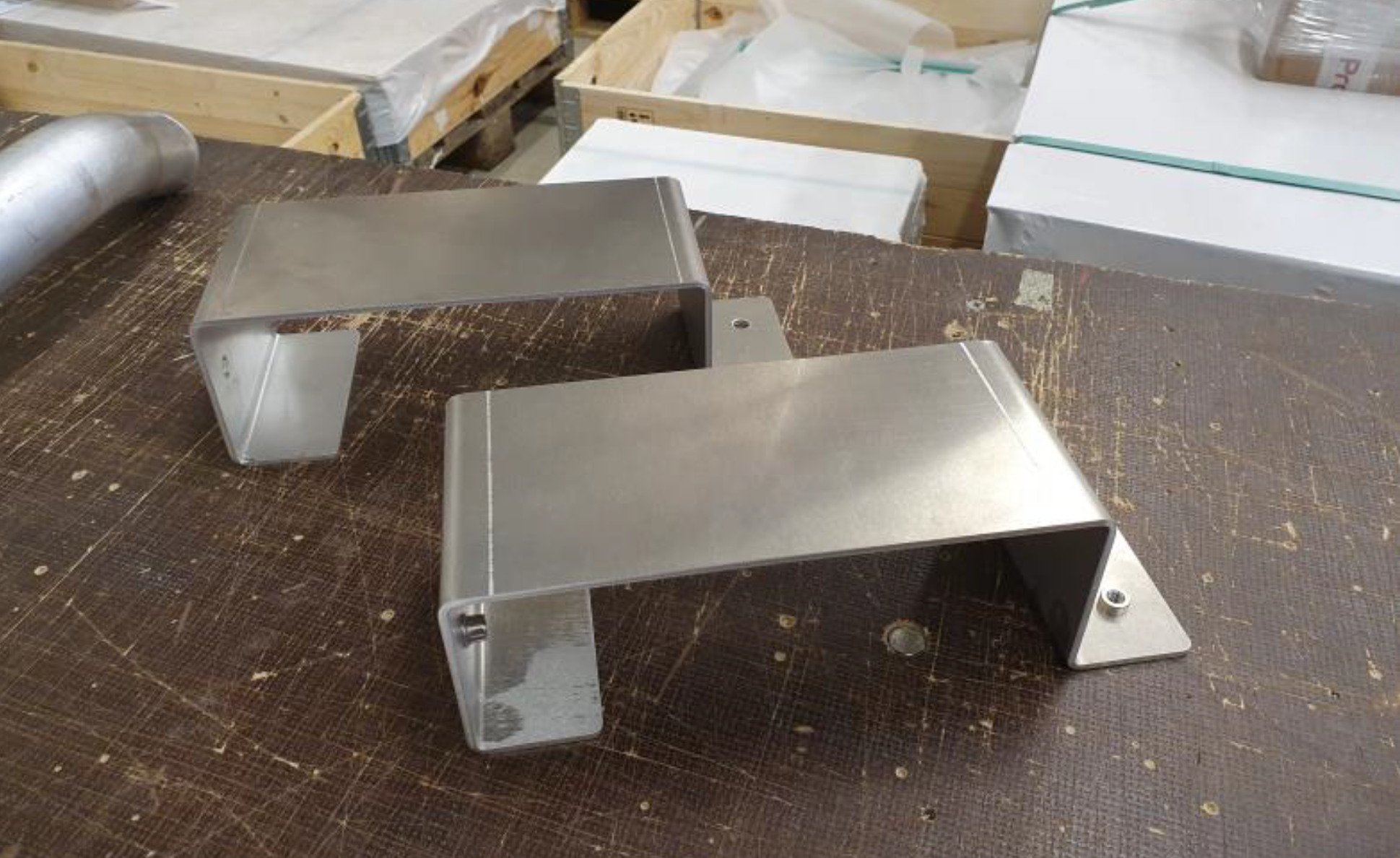
Kokeilut
Kokeiluissa Gocator 2380 -kamera asennettiin hihnakuljettimen yläpuolelle ja testikappaleita ajettiin kameran alta eri asennoissa (kuva 2). Kameran ohjelmaan ohjelmoitiin erityyppisiä mittauksia ja toimintoja, joiden avulla kokeiltiin tunnistaa, onko kappaleessa kierreniitit vai ei.
Kameran kuvausasetuksien avulla pyrittiin hakemaan paras mahdollinen tilanne kiiltävän metallin kuvaamiseen. Tämä osoittautui joissain kappaleiden asennoissa erittäin hankalaksi ja kappaletta ei saatu kuvattua tai vain osa kappaleesta tuli mukaan kuvaan. Kuvassa 3 on esimerkki siitä, että kappaleen pystyreunaa ei saatu näkymään 3D-kuvassa samaan aikaan vaakapintojen kanssa ja lisäksi mukana on osittainen heijastus.
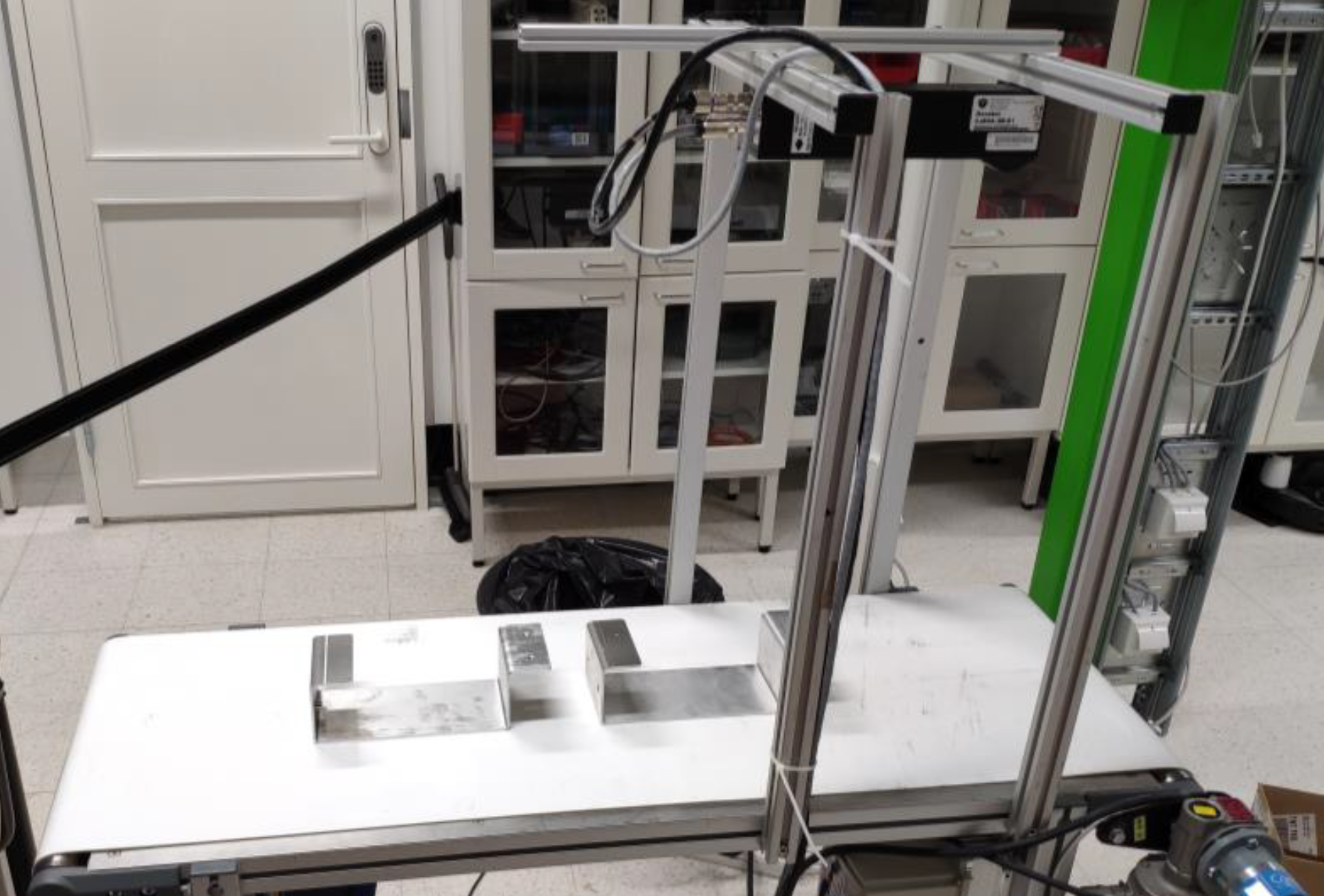
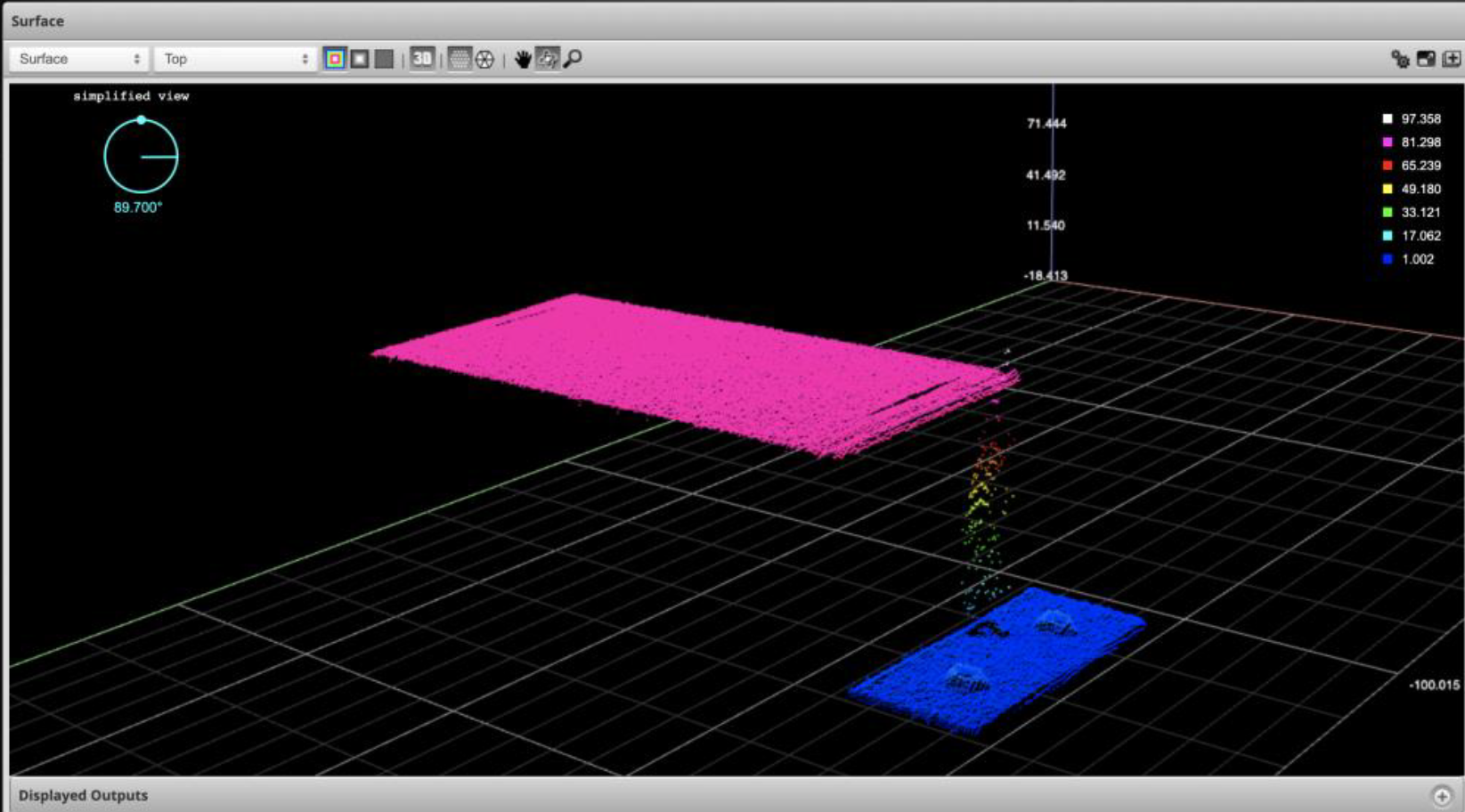
Parhaimmat kuvat testeissä saatiin, kun kuvaustilan valaistus kytkettiin pois päältä ja kuvausjärjestelmä verhottiin mustilla kankailla ulkopuolisen valon estämiseksi (kuva 4). Tällöin voitiin minimoida heijastukset. Kuvassa näkyy myös kameran projisoima laserviiva, jonka muodonmuutoksia kohteen pinnalla kamera kuvaa samalla kun kuljetinta ajetaan.
Kierreniittien tunnistamisessa parhaimmiksi ohjelmiston työkaluiksi arvioitiin reiän halkaisijan mittaaminen ja kierreniittien kohoaman mittaaminen. Reiän halkaisijan avulla kokeiltiin mitata, onko reikä niitin sisäreiän kokoinen vai niitille sopivan reiän kokoinen ja tunnistamaan näin, ovatko kierreniitit paikoillaan. Kohoaman mittaamisessa kokeiltiin tunnistaa ja mitata kierreniittien reikien kohdalta, onko kierreniitti asennettuna.
Reikien kokoa mitattaessa järjestelmä toimi välillä hyvin ja reiän koosta pystyi tunnistamaan, onko niitti paikoillaan. Ongelmaksi muodostui kuitenkin joissain kappaleen asennoissa liialliset heijastukset reiän reunoista ja sisäpinnoista, jolloin reikää ei saatu mitattua ollenkaan. Kuvissa 5, 6, 7, 8 ja 9 on esitettynä ohjelmoituja mittauksia Gocatorin ohjelmassa.
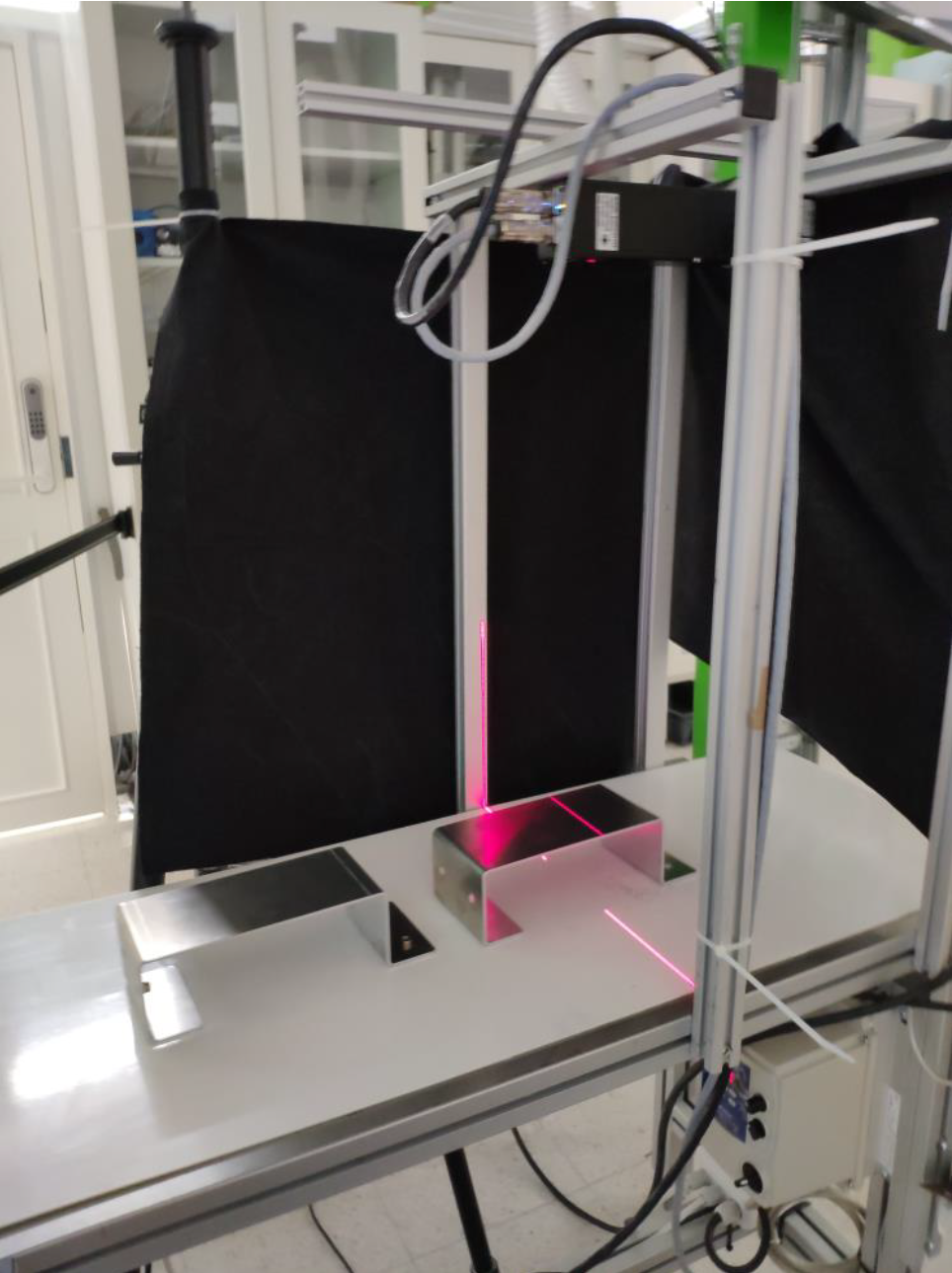
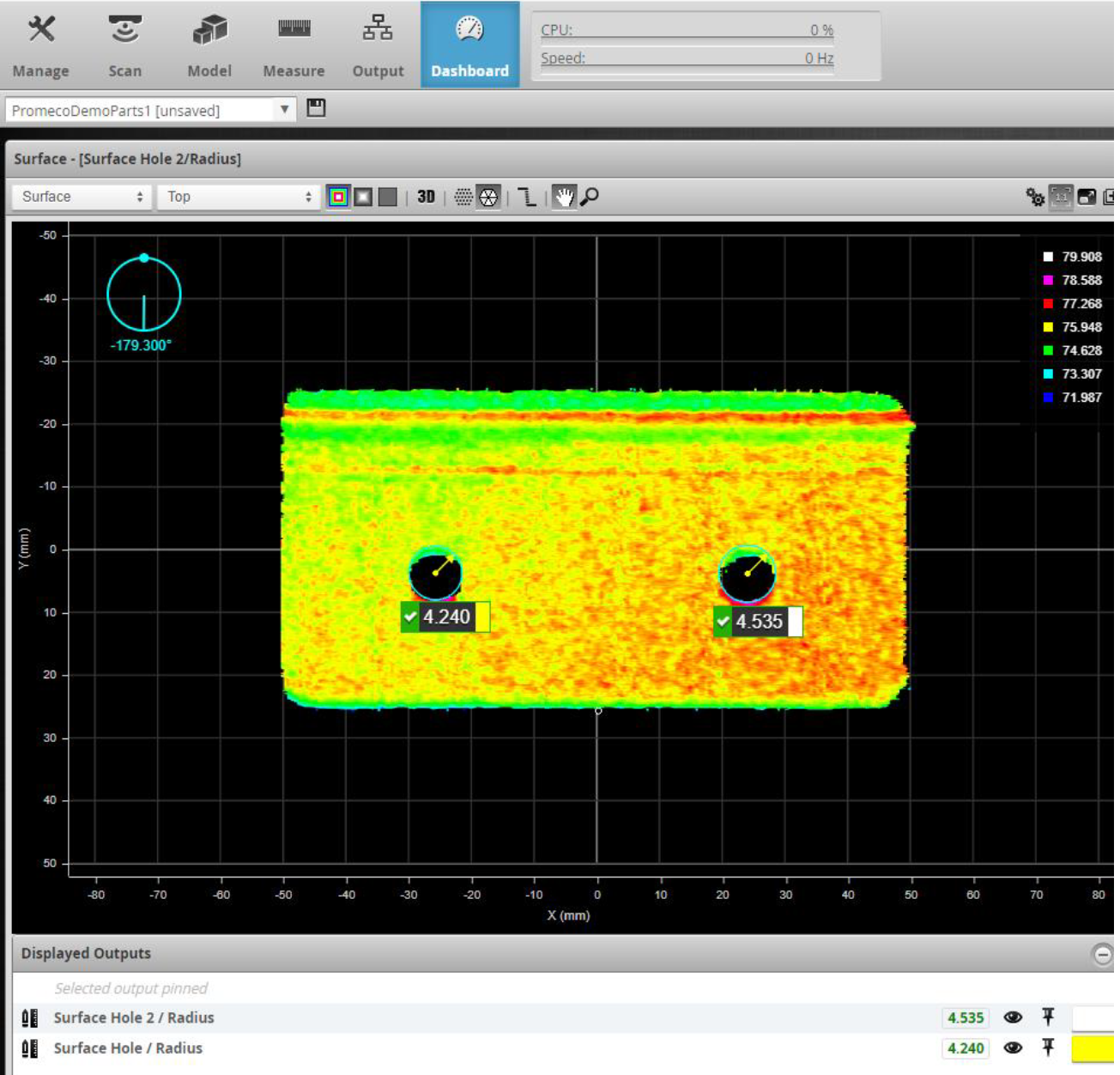
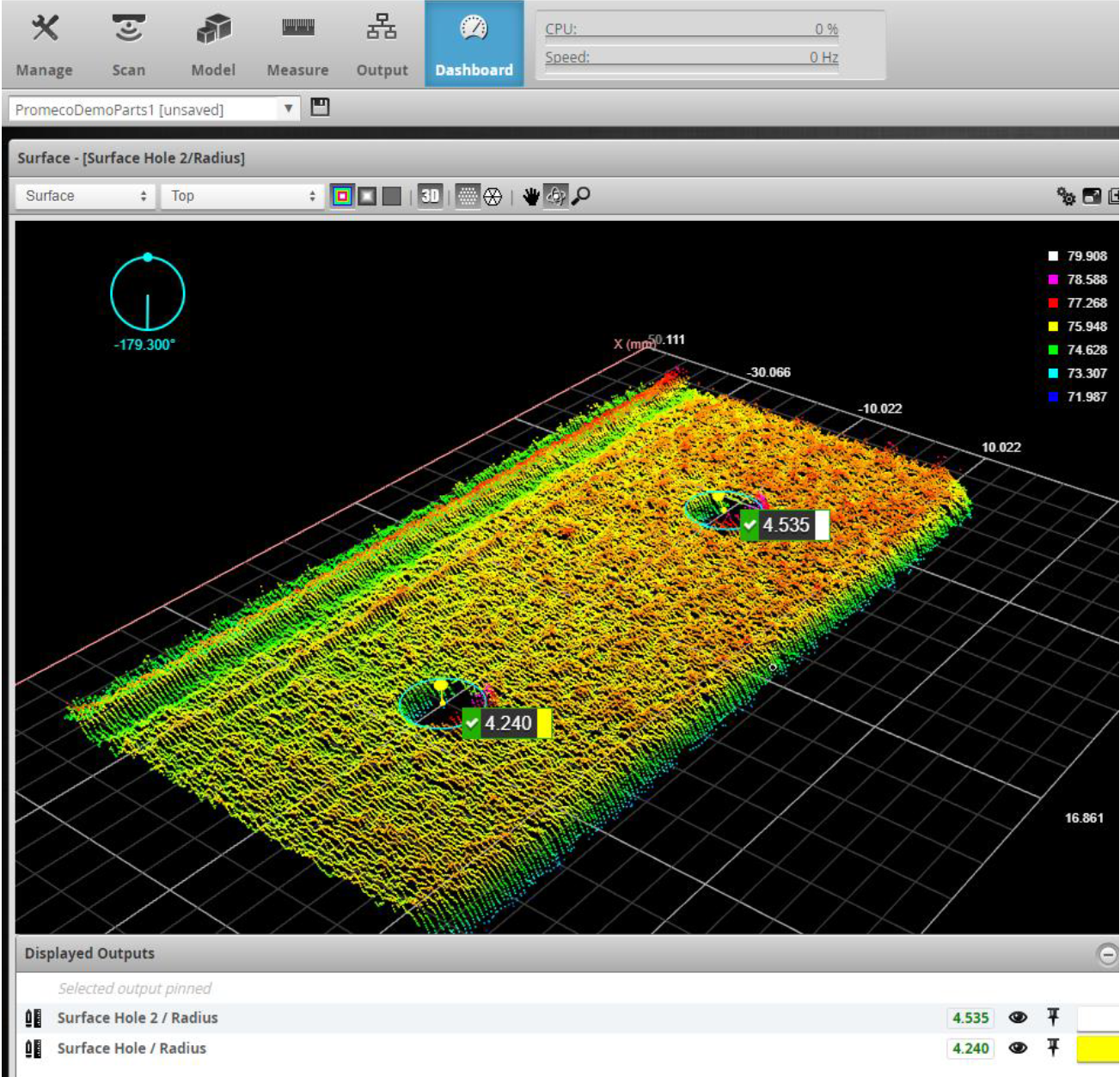
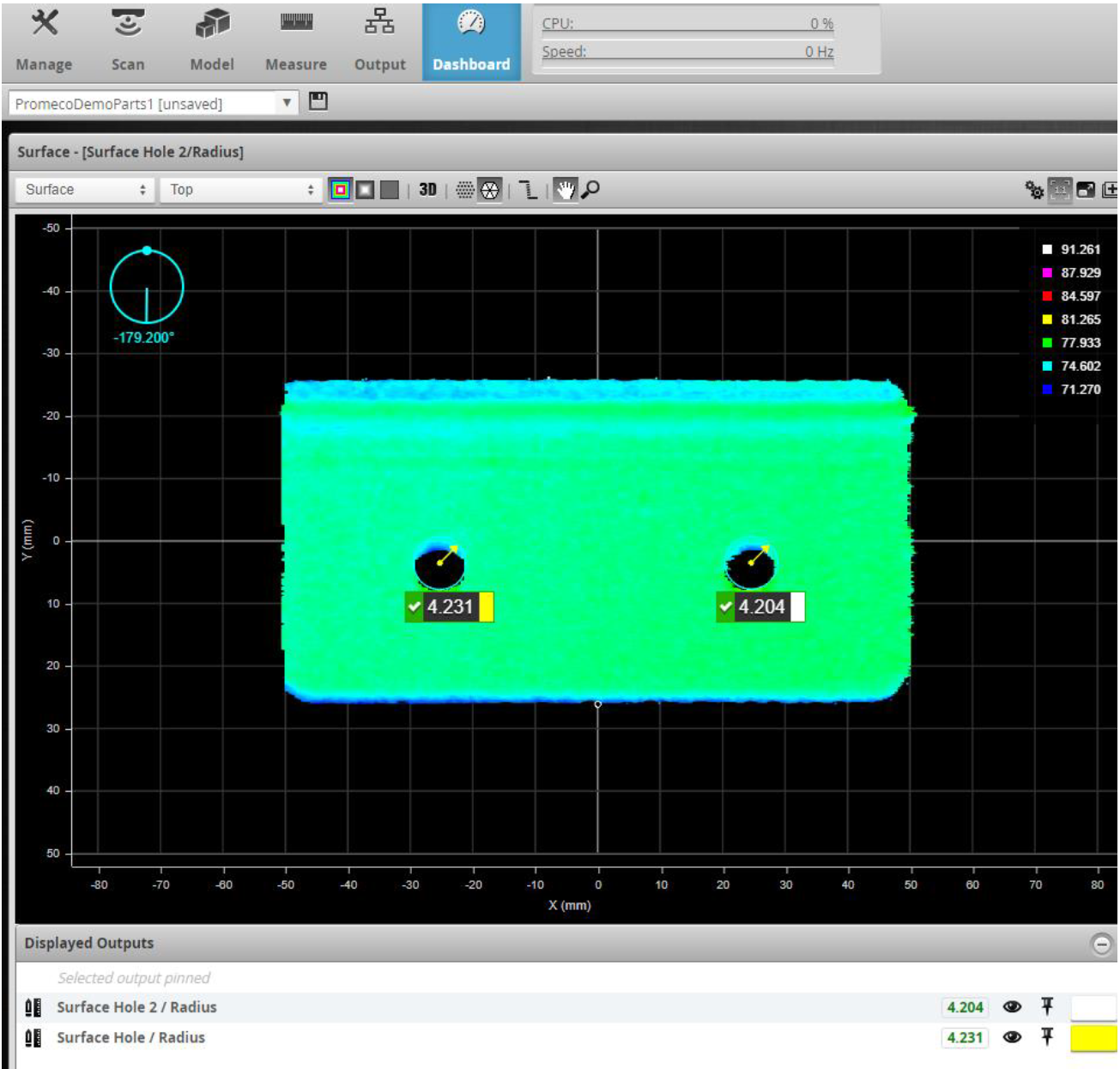
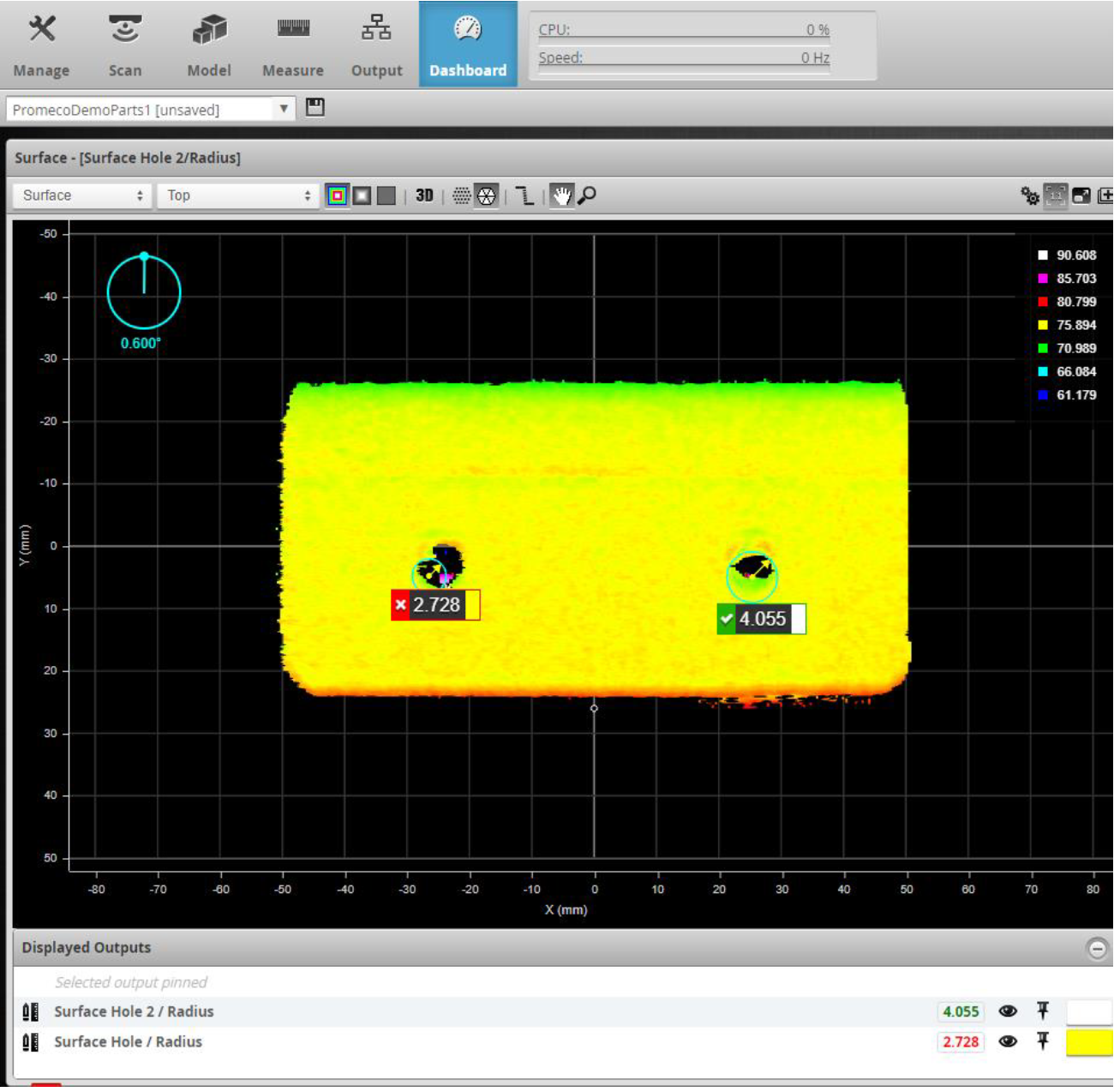
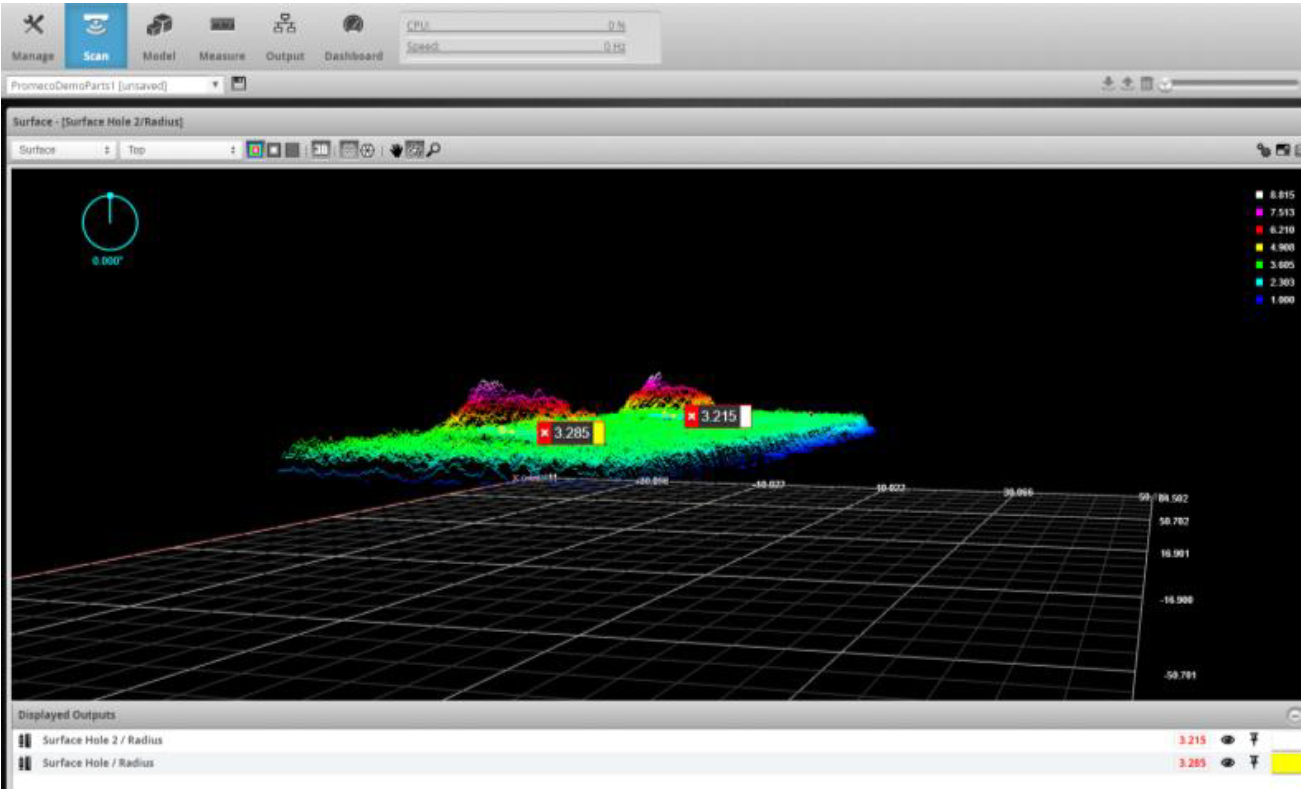
Pelkällä reikien mittauksella ei todennäköisesti pystyisi tekemään riittävän virheettömästi toimivaa sovellusta, ellei kameraa päästä liikuttelemaan parhaisiin mahdollisiin kuvausasentoihin.
Niittien muodostamaa kohoumaa mitattaessa ohjelmaan opetettiin kappaleen 3D-kuvaan leikkausraja, jonka kohdalta pyrittiin tunnistamaan asennetut niitit mittaamalla mahdollisten kohoumien korkeutta. Kohouman korkeuden ollessa riittävän lähellä 4 mm:ä oletettiin, että niitti on paikoillaan ja kyse ei ole vain heijastuksesta. Kuvissa 10 ja 11 on esimerkkejä mittauksesta.
Kohouman mittauksella voisi olla mahdollista tehdä toimiva sovellus kierreniittien asennuksen tarkastamiseen. Ongelmaksi muodostuu kuitenkin se, että testikappaleessa sisäänpäin olevia kierreniittejä ei pystytty luotettavasti kuvaamaan käytetyllä järjestelmällä. Esimerkiksi kappaleen ollessa kyljellään ei pystytty saamaan tarpeeksi eheää 3D-mallia mittausten tekemiseksi.
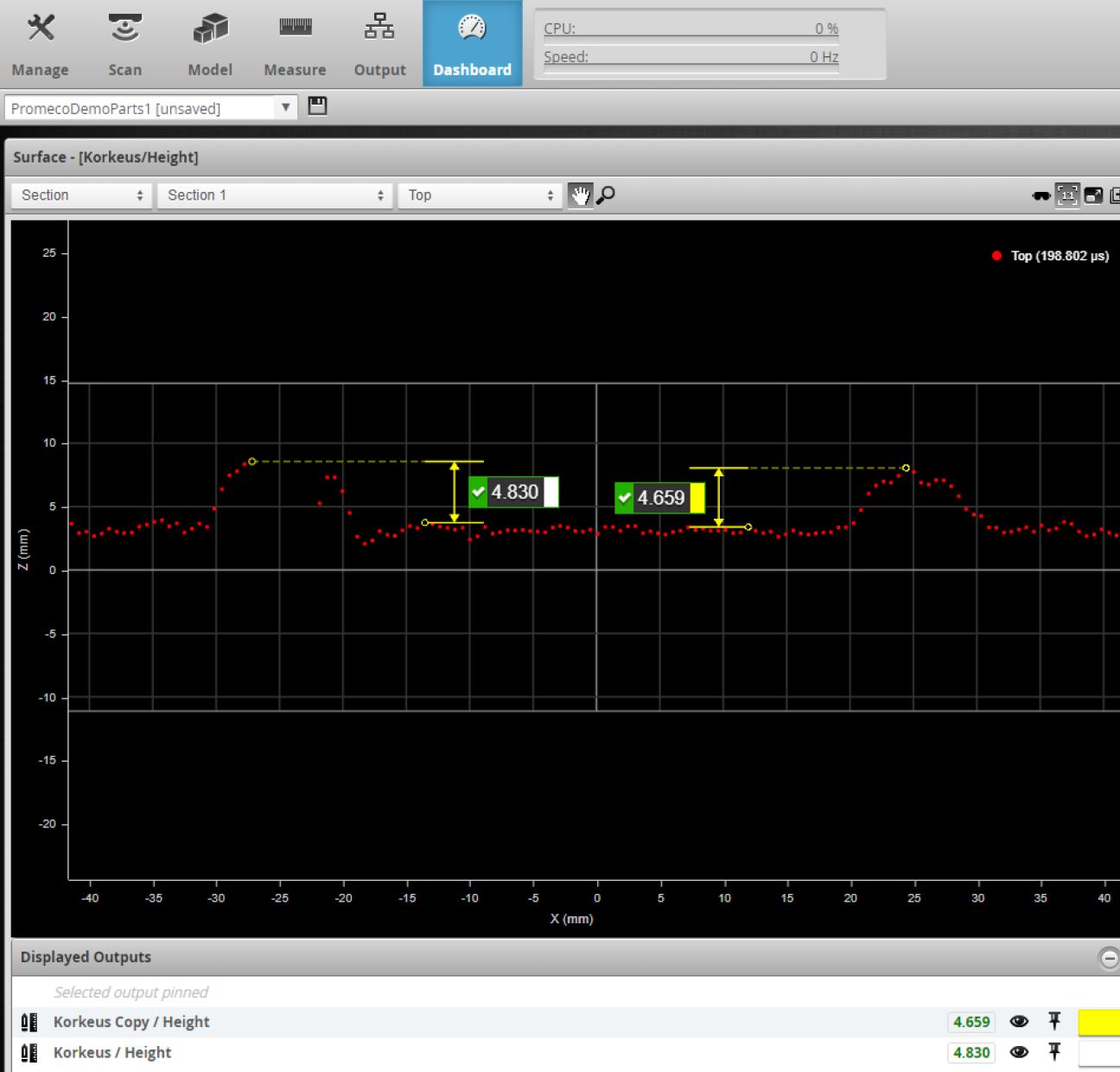
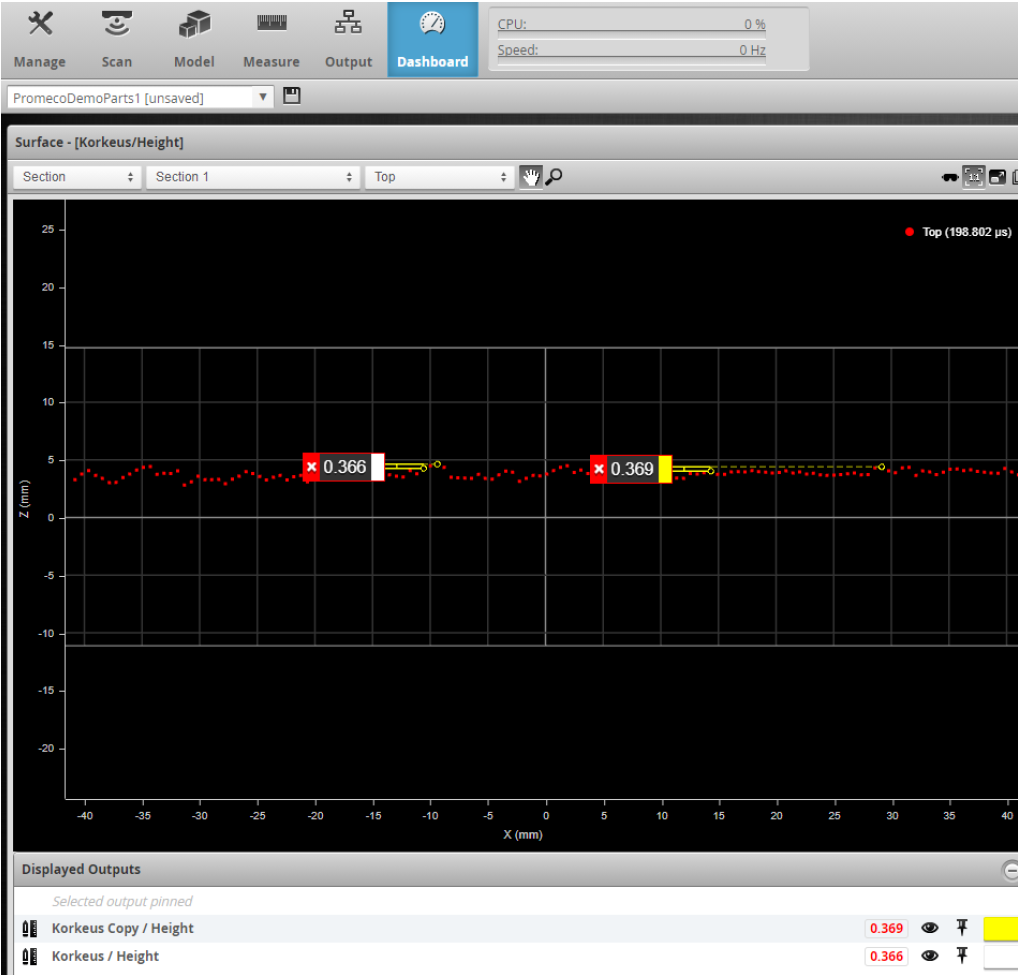
Yhteenveto
Kappaleiden haastavien ominaisuuksien ja muotojen vuoksi kokeiluja olisi hyvä jatkaa. Käytettäessä Gocator 2380 kohoumien tunnistamisessa voisi olla potentiaalia, jos Gocator olisi vapaammin aseteltavissa kuvaukseen esim. kiinni käsivarsirobotissa. Kohoumien mittauksessa tulisi kokeilla myös muita varmennuksia kuten niittien leveyden mittausta.
Gocatoria käytettäessä voisi kokeilla myös haihtuvan pinnoitesprayn kokeilemista, jos sen käyttö on mahdollista myös asiakkaan prosessin kannalta eikä lisää työmäärää/kustannuksia liiaksi. Pinnoitespray on tarkoitettu kiiltävien kappaleiden 3D-kuvaukseen heijastumien poistamiseksi. Uusiempien päivitysten mukana Gocatorin ohjelmaan on myös tullut uusia ominaisuuksia, jotka saattaisivat tuoda mahdollisuuksia niittien tunnistukseen.
Vastaavissa tapauksissa voisi kokeilla myös 2D-kuvausta. Oikein suunnitellulla 2D-kuvaukseen perustuvalla konenäköjärjestelmällä niitit voisivat olla tunnistettavissa, mutta myös tällöin kameraa tulisi todennäköisesti liikutella esim. käsivarsirobotilla oikeisiin kuvausasentoihin.